
Technological capability
TCHS owns the state-of-the-art production line system in Vietnam, with technology transferred from Hwashin Group (South Korea), including more than 600 semi-automatic and automatic machinery and equipment.
Automated and specialized production line with welding robots
The factory’s welding line is designed as an integrated module for many vehicle models, optimizing factory area and welding equipment.
Welding robots with state-of-the-art technology from Hyundai Robotics are applied in all crucial stages to:
- Improve the automation rate in manufacturing and increase efficiency and labor safety.
- Improve accuracy and product quality stability.
- Quickly adapt and transform technology to manufacture new vehicle lines.
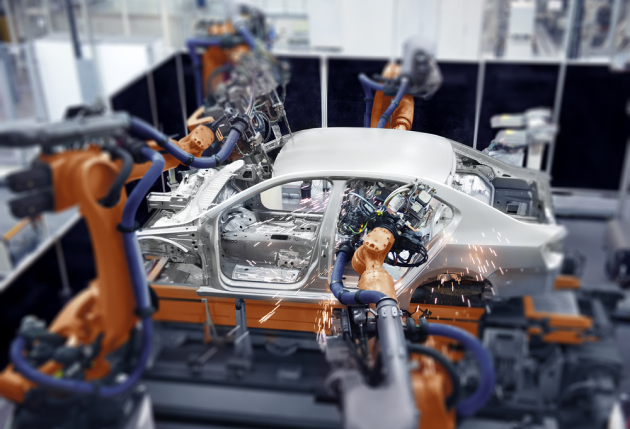
Highly complex Resistance welding technology
Spot, Bolt, and Nut welding equipment applied with advanced resistance welding methods help products achieve the highest precision and meet the most meticulous and complex manufacturing requirements.
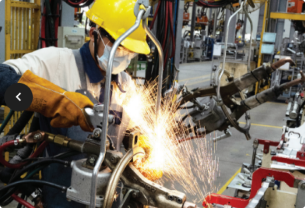
Spot welding machine is one of the main equipment and has the largest quantity in TCHS factory, creating most of the welding spots on finished products.
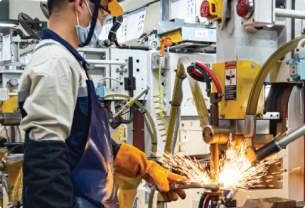
PJ welding machine is a large-capacity, semi-automatic Bolt / Nut welding machine with high accuracy based on the operation of PLCs, sensors, automatic feeding system…, thereby ensuring the best welding quality.
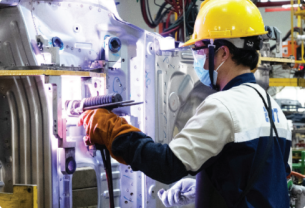
STUD Welding machine is a specialized welding machine with modern European technology, operating based on retracted arc technology. The STUD welding machine is responsible for welding bolts in difficult positions and thin surfaces.
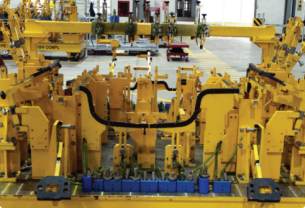
Welding jigs are the most important equipment in the assembly process, manufactured and transferred from South Korea to allow precise assembly of welded parts according to the standards of each automobile manufacturer.
Semi-automatic automotive body manufacturing process
TCHS’s semi-automatic automotive body production line is one of the most modern lines in the region today, providing absolute precision for each weld, ensuring that the automotive body reaches the highest quality according to the global standards of each automotive manufacturer.
The semi-automatic Hyundai Accent automotive body production line is the main production line at the TCHS factory, meeting Hyundai standards globally.
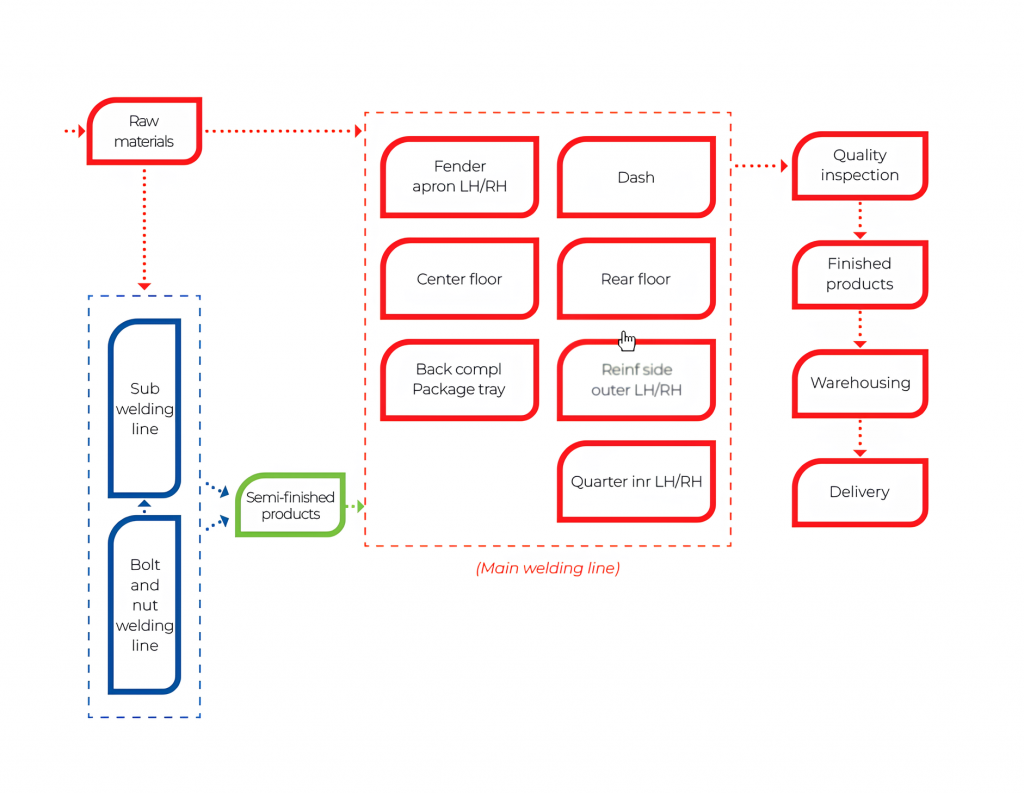
Hyundai Accent automotive body manufacturing process
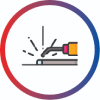
1. Materials
Sheets of corrugated iron stamped according to profile (size from 3x3cm), bolts, nuts, stickers
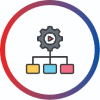
2. Bolt and nut welding line
More than 15 semi-automatic welding machines weld bolts and nuts with stamped corrugated iron sheets according to profile
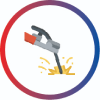
3. Sub-welding line
Welding of corrugated iron sheet parts, semi-finished products of bolt and nut welding lines together to create small assemblies (semi-finished products)
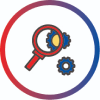
4. Semi-finished products
the final product of bolt, nut and sub-welding lines are gathered in a separate area for quality inspection, then transferred to the main welding line.
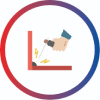
5. Main welding line
Includes 7 main lines to create 11 finished products: Joining corrugated sheet parts, semi-finished products of bolt and nut welding lines, and semi-finished products of sub-welding lines together through jigs and welded joints
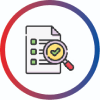
6. Quality Inspection
Inspect all products to ensure quality standards.
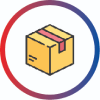
7. Finished products
The final product is created in various stages, from small pieces of corrugated iron to form 11 large assemblies, directly constituting the complete body of the Accent car.
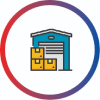
8. Storage
Finished products are stored in appropriate conditions, ensuring quality before being shipped.
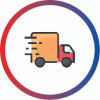
9. Delivery
Finished products are delivered to customers with quality assurance, exact quantity, and on schedule.
Quality Management System
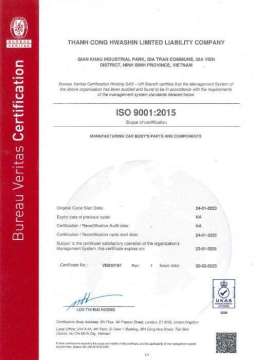
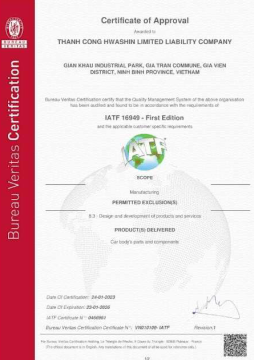
With the quality management system in compliance with ISO 9001: 2015 and IATF 16949: 2016, TCHS will be a reliable partner for automobile manufacturers and assemblers in providing high-quality automotive components and accessories, which is consistent with global standards and optimize costs.
ISO 9001:2015
ISO 9001:2015 is an international standard for quality management systems issued by the International Organization for Standardization (ISO), applicable to most fields. ISO 9001:2015 has become the world’s most widely used standard, a global standard that ensures the ability to meet quality requirements and enhance customer satisfaction in the supplier-customer relationship.
With the application of the quality management system according to ISO 9001:2015, TCHS can understand risks better, thereby providing preventive control measures and opportunities for improving and enhancing partner satisfaction.
IATF 16949:2016
IATF 16949:2016 certification is an international quality standard for automotive quality management systems, developed by the International Automobile Task Force (IATF) to ensure compliance with industry quality requirements and related partners. This standard replaces the quality standard ISO/TS 16949:2009.
To achieve IATF 16949:2016 certification, TCHS must comply with strict quality requirements, including quality management, process management, product and service control and data management and must also comply with regulations on safety and environmental protection.
Human Resources Capacity
“Human” is one of the core values of TCHS, an important foundation for the Company’s development. Therefore, TCHS continuously improves the potential of its human resources in both scale and qualifications.
Trình độ chuyên môn
Hold associate degrees or bachelor's degrees.
Unskilled workers.
Hold associate degrees or bachelor's degrees.
Personnel Structure of TCHS
Download and view portfolio
Lorem ipsum dolor sit amet, consectetur adipiscing elit, sed do eiusmod tempor incididunt ut labore et dolore magna aliqua